What's new in the maritime world
"Laney Chouest" Strongest there is!
continued from frontpage.
To support deepwater operations, which may take place more than 100 miles offshore, new generation service vessels have to be powerful, stable platforms with the ability to carry ample amounts of cargo, liquid and dry bulk mud, ballast and rig water, fuel, equipment and crew. The Laney Chouest fits the bill. Built for suction pile/anchor handling operations, it is 348 ft x 72 ft x 31 ft, with a gross tonnage of 5,900 and deadweight of 7,400 LT. It will have a fuel oil capacity of 394,260 gal, liquid mud capacity of 4,460 bbl (with 3,866 bbl spare capacity), and ballast/rig water capacity of 613,400 gal. Your father's 180-foot-long offshore supply vessel, incidentally, would fit nicely on the Laney Chouest's aft deck, which measures 183.6 ft x 56 ft with a clear deck area of 10,276 ft2. Its propulsion machinery includes four 6M43 MAK diesel engines that produce 7,250 bhp each for a total of 29,000 bhp. It will have a speed of 17 knots at normal design draft and accommodations for 58.
At a keel-laying ceremony on March 13, VT Halter Marine Inc., began the construction of the U.S. Army Tank-automotive and Armament Command?s (TACOM) newest Logistic Support Vessel. We value the confidence and trust that the U.S. Army has placed in our company and our employees,? said Butch King, CEO of VT Halter Marine. ?Our employees have first-hand experience in designing and building Logistic Support Vessels, Large Tugs and LCU-2000 Class Landing Craft that are specifically tailored to operational requirements. The U.S. Army is a long-term marine customer and about 50 vessels in their fleet have been built at our shipyards. We are very proud of the fact that this vessel will be used to help support our fighting forces and guard our national interests.? The 313-ft. LSV class vessel, designed to carry over 2,000 tons of deck cargo, has a beam of 60-feet and a molded depth of 19-feet. VT Halter Marine announced the Logistic Support Vessel (LSV) contract award December 20, 2002. Vessel delivery should take place sometime during the fourth quarter, 2004.
Sonsub notes record pipe lay
Sonsub's I10 and I11 ROVs assisted a pipe lay set at 2,175 m, said to be a world record, during the Canyon Express project in the Gulf of Mexico. Both ROVs working off SaiBos's FDS conducted more than 200 dives logging more than 3,500 hours between the two, with I10's longest dive at 143 hours and I11's longest at 201 hours. The ROVs performed touchdown monitoring up to 650 m behind the vessel, bathymetry, and pipe tracking survey. They supported the mud mats and inline sleds settings. The company's I3 and I12 recently helped install a dozen hydraulic leads on the same field. The ROVs latched onto the 800-lb leads and flew them to their locations for installation from the MSV Maxita. Electrical leads installed included a hybrid of fiber-optic end connectors. TotalFinaElf operates the Canyon Express field. Sonsub agreed to supply tooling for the project and to assist with a single methanol distribution line and two 12-in. installed flowlines and electro-hydraulic umbilical installations in up to 7,200-ft water depth. The umbilical system controls four subsea wells at the King's Peak field, three to four subsea wells at the Aconcagua field, and two subsea wells at the Camden Hills field.
Truss Spar for Murphy Oil. Murphy Oil Corporation has awarded a contract to J. Ray McDermott, Inc. to construct a floating production system for the Front Runner project on Green Canyon blocks 338 and 339 in the Gulf of Mexico. J. Ray McDermott subsidiary SparTEC Inc. will be the general contractor responsible for engineering, procure- ment, construction, and installation of the Spar. The Front Runner partners have approved a plan for developing the area using a truss Spar capable of handling 60,000 b/d of crude oil and 110 MMcf/d of natural gas. First production is targeted for the first half of 2004. Murphy operates Front Runner with 37.5% interest. Partners are Dominion Exploration & Production, Inc. with 37.5% and Spinnaker Exploration Company with 25%.
Subsea 7 has been awarded a 30M US dollar subsea installation contract by the joint venture company Modec International LLC, for the development of Bijupira/Salema fields. The two fields, which are operated by Enterprise Oil Operations Limited, are located adjacent to each other in offshore Brazil Campos Basin, approximately 174 miles from Rio de Janeiro, in water depths ranging from 1,575 feet to 2,890 feet. The contract comprises subsea installation of the fields development including FPSO (Floating Production Storage & Offloading unit) installation. The subsea part of Bijupira field will comprise two production manifolds, one water injection manifold, one gas lift PLET (Pipeline End Termination) and one UTA (Umbilical Termination Assembly), eight inch production flowlines, a seven inch water injection line and a five inch gas lift line between location and the FPSO, all 18 km in total approximate length and associated jumpers. The contract will be managed and operated from Subsea 7 base facility in Rio de Janeiro by the locally based team with support from the group international resources and Brazilian content for the overall installation project will be substantial. Subsea 7 assets that will be used to carry out the work will be the flexible lay vessels, Toisa Perseus and the K3000 or Lochnagar. Vessel activity will commence Nov. 02
The partners will jointly fund the project, which was initiated by the offshore industry after a number of supply vessel incidents. The new DNV led research and development project, called Bridge Design Offshore Service Vessels (NAUT-OSV), comes as a response to the offshore industry's safety concerns. The aft bridge of a supply vessel is where an operator controls the ship when close to quays or platforms, in addition to winches and other loading tools.
The SOLAS (International Convention for the Safety of Life at Sea) does not regulate in detail the layout of a supply ship bridge and the aft bridge is not regulated at all. This has caused the designs to vary to a large degree, often causing an imperfect working environment. The aim of the project is to introduce the DNV NAUT-OSV guidelines as part of the standard charter requirements.
World record achieved on Horn Mountain SPAR installation
Heerema Marine Contractors has established a world record during the installation of an offshore SPAR mooring system. The BP Horn Mountain SPAR project set the new record with its mooring line system, which was installed in 1,650m (5,500ft) of water off the Gulf of Mexico. The SPAR project, installed in two phases, saw the world record broken during the first phase of the project, with the installation of the mooring line system. The mooring line system consists of nine piles, each pile being 5.5m in diameter and 27m long. The length of each mooring line is 2,300m and is made up of three sections, a single section consisting of 75m of chain link (each link being 14cm in diameter)and two sections of heavy steel wire also 14cms in diameter. The world record breaking project was the first project to be carried out by the semi-submersible construction vessel Balder after its deep water conversion.
Torch Offshore gains ISM certification. Torch Offshore has announced that it has been awarded ISM Certification by the American Bureau of Shipping (ABS). The Safety Management System of the Company was audited by the ABS and was deemed to be compliant with all of the requirements of the International Management Code for the Safe Operation of Ships and Pollution Prevention (ISM Code) as adopted by the International Maritime Organization. ISM certification was granted after a thorough audit of the company's pertinent records, interviews with company personnel and observation of daily activities.
Cal-Dive unit acquires DP vessel The specialized, dynamically positioned vessel Seawell is being transferred by CSO Ltd. to Well Ops (U.K.) Ltd., a wholly owned subsidiary of Cal Dive. The transfer is part of a deal that sees Technip-Coflexip disposing of its Subsea Well Operations Business Unit to Cal-Dive. The transaction, valued at .5 million, is expected to close within days and is in line with Technip-Coflexip's program to dispose of non-strategic assets during the coming 12 months.
Under the terms of the agreement, CSO Ltd. will transfer to all activities and resources dedicated to Subsea Well Intervention, including Seawell, to Well Ops, as well as assigning current client and vendor contracts. Purpose built for well operations, the Seawell, a 111-meter, DP3 vessel, was recently upgraded for coiled tubing deployment and well testing.
Engineering, project management and specialized CSO Ltd. personnel dedicated to its Well Operations Business Unit will join Cal Dive. To smooth the transition, CSO Ltd. will provide, for an interim period, a number of support services, particularly in the areas of vessel management and diving support. In return, the vessel will be made available to CSO Ltd. through a cooperative agreement to support its contracting needs. Tom Ehret, President of the Offshore Branch of Technip-Coflexip, declared, "In the late eighties, we created the technology and operation of subsea well operations from a dynamically positioned monohull vessel. Since then, this business line has gained full market acceptance, and our Subsea Well Operation Business Unit is the clear leader in this segment. Today, within the broader context and strategy of the Technip-Coflexip Group, this activity is no longer part of our core business. We are therefore very pleased to announce this agreement with Cal Dive, and we believe that Cal Dive is very well placed to pursue and further develop successfully these well operations activities."
Owen Kratz, Chairman and CEO of Cal Dive, commented, "This acquisition emphasizes the commitment of Cal Dive to be the leading and dominant provider for the industry's needs in the developing subsea well service market. Combining the subsea lubricator (SIL) based technology developed by Technip-Coflexip with the riser-based technology being pioneered by Cal Dive's Q4000 greatly enhances the ability of CDI to deliver the best subsea solutions for our clients. We are pleased to be able to work with CSO Ltd. in consummating this acquisition, which illustrates the mutually beneficial relationship between the two companies." With a workforce of about 18,000 and annual pro-forma revenues of nearly 4.5 billion euros, Technip-Coflexip ranks among the top five in the field of oil and petrochemical engineering, construction and services. Headquartered in Paris, the Group is listed in New York (NYSE: TKP - News) and in Paris (EURONEXT: 13170). The main engineering and business centers of Technip- Coflexip are located in France, Italy, Germany, the UK, Norway, the Netherlands, the United States, Brazil, Abu-Dhabi, China, India, Malaysia and Australia. The Group has high-quality industrial and construction facilities in France, Brazil, the UK, the USA, and Finland as well as a world class fleet of offshore construction vessels. Cal Dive International, Inc. headquartered in Houston, TX, is an energy service company specializing in well operations and subsea construction. CDI operates a fleet of technically advanced marine construction vessels and robotics, and conducts salvage operations in the Gulf of Mexico. Energy Resource Technology, Inc., acquires and operates mature and non-core offshore oil and gas properties. Simmons & Company International Limited, the specialist energy industry investment bank, advised Technip-Coflexip on this transaction. Creating a Portable Dynamic Positioning System Imagine being able to take something as a simple as a barge, and convert it into a highly sophisticated dynamically positioned vessel. Now, imagine this conversion being done dockside, in the water, in a week's time. Thrustmaster's deck-mounted Portable Dynamic Positioning System (PDPS) Horizon, Cal Dive Form Joint Venture Horizon Offshore, Inc. has entered into a letter of intent with Cal Dive International, Inc. (CDI) to conduct reeled pipelay projects in deepwater areas of the U.S. Gulf of Mexico. The two companies will jointly fund construction of pipelay equipment to be used in conjunction with CDI's Cal Dive Acquires Interest in Deepwater Vessel Cal Dive International, Inc. and Aker Marine Contractors, Inc. (AMC) have acquired Hvide Marine's majority equity interest in the new million Dove anchor handling and subsea construction vessel. The dynamically positioned Dove is scheduled to finish sea trials in mid-July Read the full stories on www.marinelink.com
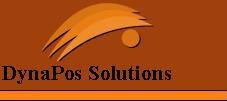
|
News
Alstom to Equip DP Platform Supply Vessels
Alstom has been awarded a million order to supply equipment for 10 new platform supply vessels which are being built in the U.S. Bender Shipbuilding & Repair Co. Inc. of Mobile Ala., awarded Alstom the contract to design, install and commission the fully integrated AC electrical propulsion and control systems for the 210-ft. support vessels which will be based in the Gulf of Mexico. Alstom will also provide support and training at its technical training facility in Houston, Texas. The equipment includes Class II DP systems from Alstom's 'A' Series and vessel control systems, as well as switchboards, transformers and AC variable speed drive trains. The switchboards will be built in the US, allowing flexibility during the design phases of the project. Steve Raynor, Sales Director for Alstom's Marine and Offshore Activity, said: "We secured this significant contract based on our proven record with Bender Shipbuilding, having completed a number of orders for them in the past. We were also the only company which could serve as a single source supplier for all the DP, vessel management system and propulsion equipment and provide full support through our training facility in Texas." The first vessel is due to be delivered in March 2004
Early in 2Q 2002, Noble announced it would purchase two semisubmersible rigs from Transocean. With the transaction finalized, Noble plans to upgrade the Transocean 96 and Transocean 97 to make them suitable for deepwater work. The semis, last upgraded in 1997, are both pentagon design rigs capable of operating in 2,350-ft water depth. Plans call for an investment between million and million per unit for refurbishments and upgrades.
Statoil's Siri platform is set to host three new Danish sector developments. State oil company DONG has submitted plans for its Cecilie and Nini discoveries to the Danish Energy Agency. These call for an unmanned wellhead platform on each of the fields, which have combined oil reserves of 65 MMbbl. Pipelines would be installed between the two platforms, and to Siri, where the oil would be processed. Siri is located 10 km from Cecilie and 31 km from Nini. Development costs are put at just under million, with a probable start to production next summer. Simultaneously, Statoil plans to develop the much smaller Siri East segment 1 via two subsea wells tied back to the Siri platform. A water injection line could be installed to serve both Siri East and Nini. Statoil would also likely place a subsea water injector on Stine, the western segment (2) of Siri East, which it brought on-stream this January via an extended-reach well from the Siri platform. In time, DONG is expected to assume operatorship of the Siri license as owner of the bulk of the incoming oil. It is also examining the possibility of laying a new westbound trunkline to take gas to the UK from Danish sector fields.
Most would more than likely offer a collective groan of discontent by this suggestion since they often spend more than four months at sea in one given shot. Time spent away from relaxation with their families is precious to these individuals as it is hard to come by. Therefore RTM Star (Simulation, Training, Assessment & Research) Center, located in Dania Beach, Fla. And Toledo, Ohio, strives to give students who come to the training center an atmosphere that exudes a "home away from home" environment. Driving along the industrious thoroughfare of U.S. 1 (or Federal Highway, as the locals call it), stands a building on the corner of West Dixie Highway that could easily be mistaken for a country club. Entering RTM STAR Center's Dania Beach, Fla. facility, guests and students are greeted by tall palm trees, maintenance people on golf carts and neatly lined and labeled guest rooms (125 to be exact), as well as an outdoor swimming pool, exercise facility and movie theatre. The facility also boasts what it is the largest and one of the most comprehensive training facilities for merchant mariners and officers. The Center is always researching its course offerings to offer students the most up-to-date classes, and is home to the world's only 360-degree Full Mission Bridge Simulator, which is complemented by the center's Slow Speed and Medium Speed Diesel Simulators. The Bridge Simulator, which provides an immense 360-degree view of real-time, at-sea situations, is an invaluable training tool that features a Litton Sperry 2100 Integrated Bridge System (IBS) similar to the one found on RCCL's Voyager of the Seas. This one-of-a-kind device boasts podded propulsion capability, as well as Dynamic Positioning (DP) capability, and is set off by the Center's 250-degree bridge simulator. Walking into the simulation room, is much like stepping into a virtual reality-type ride at Epcot Center in Disney World. Star Center made MR/EN right at home by displaying a real time at sea "scene" of New York Harbor complete with the Verrazano Bridge, Liberty Island and Governor's Island in the distance. While officers command the controls of the simulator, simulator operators located in an adjacent room throw many situations in their directions many that could be life threatening or pose imminent danger. When MR/EN visited Star Center, the operators provided a scenario on a tanker traveling through New York Harbor in both the day and evening. In the vessel's field of vision lay the New York skyline, as well as several types of ships cruising through the harbor on a busy day. The simulator operators threw anything and everything in the tanker path, from small sailboats to U.S. Navy destroyers to containerships, and could include, for example, a U.S. Coast Guard helicopter cruising overhead looking for landing spot, or a bevy of media helicopters covering a high-publicity event, such as Fleet Week. The officers at STAR Center even go as far as to communicate to the students via "staged" traffic on the simulator's radio. According to Graeme Holman, STAR Center's head of Customer Service & Operations, the simulator is capable of running a variety of situations. "The simulator can be changed from port to starboard side, can mimic an oil spill and even change the wind and current speed. Mariners who are trained on this system will always say that this is how a ship is handled in real time situations." Evolution of a Major Training Facility Since opening its doors to the maritime community in the winter of 1993, STAR Center's three-story building at its Florida facility has expanded rapidly, an expansion which includes additional floors on the original building and the commencement of operations in Toledo, Ohio for training on inland waterways and Great Lakes. STAR Center is preparing for the grand opening of its new waterfront training facility located in Fort Lauderdale just minutes from its Dania Beach facility. While fast craft training is not new to STAR Center, according to Jerry Pannell, head of STAR Center's Deck department, the center, (which in the past had to rent out fast rescue craft from a shore-based facility), will now have this "self contained facility" approximately 2.5 miles from its main training grounds. The new center, which at press time was scheduled for a mid-August opening, will house one 18-ft. (5.5-m) and two 26-ft. (8-m) fast rescue boats, a single-point davit for launching and recovering boats, enclosed SOLAS certified lifeboat, davit launchable liferaft, as well as classrooms and workshops. Designed to meet STCW '95 compliant training, and are U.S.C.G. approved, the curriculum followed at this new center will focus on Proficiency in Fast Rescue Boat and Proficiency in Survival Craft. A spitting image of a diesel electric engine onboard a traditional cruise ship, the Center' Full Mission Diesel Electric Engineroom Simulator puts the "real" in real time as it is based on a large cruise ship running on 40 MW of power at 6,600 volts. When MR/EN was hosted by Dwight Hutchinson, STAR Center's director, Quality and Engineering, he explained how students operate the simulator's controls, which run on Kongsberg Maritime Ship Systems (KMSS) software. The simulator, which is actually the former engine plant from the cruise ship Sun Princess, boasts four diesel generator sets connected to two 14 MW synchronous propulsion motors. Four thrusters and two emergency generators are also part of the simulated vessel's power package based on a 77,000 grt with a cruising speed of 18.5 knots. Hutchinson also mentioned that this past May, STAR Center has furthered its commitment to providing the highest grade of advanced training via its recent transition to ISO 9000:2000 certification. This award, which was granted by the Center via a third party conversion audit by Det Norske Veritas, recognizes the Center as the only training facility in the U.S. to hold this type of certification. While the staff at STAR Center realizes that the certification puts the facility in a high regard, it also translates to more time researching and upgrading its curriculum and programs. This, however is not foreign to the facility, as its instructors and full time staff already have a handle on this specifically Capt. Al Stiles, who is the Center's Curriculum & Program Development Dept. Head. According to Stiles, approximately 60 percent of the Center's course offerings are cruise-oriented, and, as always, have been tailored to meet the requirements of each individual cruise line.
According to Kevin Peters president of Miami Diver, there was no doubt in his mind that the alliance would not have been an immediate success. "Because of this venture, we now have more locations and more trained personnel to serve the cruise industry," Peters said. The Subsea Solutions Alliance has responded to and carried out emergency repair for cruise ships from Miami to Alaska, from Europe to Australia and Asia. Recently through members of the Subsea Solutions Alliance a blade change was carried out on a cruise ship in the Port of Venice, a stern seal repair was done on another cruise ship in Alaska, a stabilizer repair on another cruise ship in Peru, a propeller repair in Miami along with a bowthruster repair for a cruise ship in Australia. While Peters' goal is of course to provide state-of-the-art repair solutions that are cost-effective, he would also like to continue providing cruise lines with maintenance support of their fleets. "Our focus for the last 10 years has been on cruise ships," Peters said of Miami Diver. "Since many of these vessels were built in the 1980's, they will need to be maintained. In addition, many experimental, or innovative equipment has been added so therefore more problems could occur, and when this happens, the Subsea Solution Alliance will be called. Gone are the days where a ship had to go into a drydock and risk missing precious moneymaking days at sea. A quick call to any of the Subsea Solution Alliance members allows the vessel to have all its work completed, with out delay to the vessel. Depending upon the complexity of the job the personnel may travel with the vessel and perform repairs while the vessel moves to a variety of ports. An example of this was (from March 22 - April 9, 1996) when wake modifiers were installed on the trailing edges of the primary strut arms on a new cruise ship that was experiencing a "singing" noise that could be heard inside the staterooms. The noise, according to Peters was the result of a design flaw in the vessel's strut during original construction. As the vessel pulled into various port locations, such as San Juan, St. Thomas and Santo Domingo, the divers went to work beneath performing hyperbaric weld modifications in accordance with the vessel's classification society Det Norske Veritas. Each day, divers would begin welding the wake modifiers by stripping down the coating system on the trailing edges of the primary struts down to the bare metal, via the use of hydraulic grinding tools. Once the welding procedure was completed, each trailing edge piece was allowed approximately two hours cooling time while covered with an asbestos blanket. Each weld seam was then examined with magnetic particle where it revealed no signs of irregularities deeming the vessel ready for regular operation. Another great benefit of the Alliance other than having a larger group of highly skilled technicians available world wide is that repair work in progress can start in one Alliance members area and be completed in another Alliance member's area. For example, recently a cruise ship called Miami Diver with concerns about the vessel's bowthruster. Miami Diver carried out the initial inspection, diagnosed the problem and presented a repair procedure and schedule that would work in conjunction with the vessel's schedule. The second part of the repair was carried out in L.A with Miami Divers L.A. office and finished in Vancouver and Alaska by the All-Sea office in Vancouver. What Does The Future Hold? The Subsea Solutions Alliance has recently developed equipment and procedures to carry out stern seal replacement underwater. To date several cruise vessels that have experienced stern steal problems have been able to avoid unscheduled dry-docking by utilizing the Alliance's underwater stern seal repair systems. The Subsea Solutions Alliance via Miami Diver is the authorized underwater seal repair facility for Blohm+Voss in Germany. In addition the Subsea Solutions Alliance performs underwater straightening of ship propellers world-wide as network members of Lips Propellers exclusive underwater repair licensee Subsea Propeller Inc Through Miami Diver the Subsea Solutions Alliance also plans to put maintenance contracts in place with several of the major cruise lines, and already has a commitment from Royal Caribbean to perform propeller polishings on their vessels every six months. According to Peters, the benefit of this simple maintenance task provides the owner with a significant amount of fuel savings, as it lessens the amount of fossil fuel burned by the vessel. The Subsea Solutions Alliance performs "check ups" on each cruise vessel simply by having its divers do a swim out report on major mechanicals such as thrusters, fins and propellers. "The dive out reports can prevent problems before they start," Peters said. "If we find something that we think could be a potential problem, our divers let the owners know how they can fix it." The Alliance is presently involved in underwater security inspection and is in conversation with several major cruise ship companies to provide underwater security inspection world-wide.
--------------------------------------------------------------------------------
Trico Marine Services, Inc., has taken delivery on the Northern Canyon, a 279-ft. UT 745 design platform supply vessel (PSV). The state-of-the-art vessel is designed to serve deepwater markets worldwide. Built in Norway, the Northern Canyon is equipped with a DP2 (dynamic positioning) system and is among the largest, most technologically advanced PSVs available in the industry. The vessel, which will be deployed initially in the North Sea, is quipped as a remotely operated vehicle vessel to perform subsea construction work globally. It has been awarded a three-year contract by Canyon-Offshore, Inc. Trico is scheduled to take delivery of a second 279-ft. PSV in September 2002. It also expects to take delivery of three new generation 155-ft. crewboats designed to transport personnel and oilfield products and supplies to offshore drilling and production platforms during the fourth quarter of 2002 and the first quarter of 2003.
Design contract awarded to Skipsteknisk Skipsteknisk AS in Norway has been awarded a design contract for a new ROV survey vessel by Ostensjo Rederi AS in Haugesund, Norway. The contract is a result of a close co-operation between the two companies and the ship to be built is a new design, theST 253.
At 85m overall and with a breadth of 18m the ST 253 will be arranged for various types of surveys, including handling of ROVs, sub-sea installation work, and execution of geo-technical surveys. She will be equipped with a diesel electric propulsion system, dynamic positioning, helicopter deck, moonpool and a large heavy-lift crane on the aft deck.
Following commissioning early in 2003 she will be chartered to DeepOcean and will work for Norsk Hydro. Kongsberg Simrad AS and ABB AS have entered a worldwide co-operation agreement on joint marketing, sales and technology development to marine and offshore vessels. As part of this agreement there will be a transfer of ABB's business related to dynamic positioning to Kongsberg Simrad. The two companies have established themselves as leading international suppliers with complementary products and systems and say they aim to become the leading vendor of vessel automation systems, dynamic positioning, electric power, propulsion, and thruster systems to marine and offshore vessels.
The SSPA Dynamic Position Predictor is a highly advanced navigation aid, to be used for continuous dynamic position prediction within 30-600 seconds. The bridge officers will be able to steer and control the ship in a safer and more accurate way, as the ships contour, presented in 3 different predicted positions ahead, is visualized on the ECDIS display. The DPP is customised for each individual ship. An advanced mathematical model of the ships hydrodynamics is used for calculation of the ships predicted positions, based on the adjustable timestep selected by the officer. Output data from the dynamic predictor are given for T, 2T and 3T seconds ahead and comprise the ships course, speed and position. The DPP can be delivered either as a software package, to be implemented in an integrated bridge system, or as a separate unit communicating with the bridge system by use of serial interface NMEA 0183. ExxonMobil employs innovative strategy to accelerate deepwater developments Exxon Mobil Corporation has announced that it will utilize an innovative, generic FPSO (floating, production, storage and offloading) concept to accelerate the production from new deepwater fields. The FPSO vessel is designed as an Early Production System (EPS) and will allow the company to economically develop offshore resources with less development time between discovery and first production. Construction is underway for three EPS FPSOs for useoffshore West Africa. The first of these, the FPSO Falcon, is expected to leave Singapore in late summer 2002 and will be used for the Yoho development offshore Nigeria. "The Early Production System offers a significant shortening of time between discovery and oil production by as much as two to four years," said Morris Foster, president, ExxonMobil Development Company. "This strategy provides us greater flexibility for future offshore developments, and reduces costs by standardizing one design and utilizing nearly identical equipment from one vessel to another. By utilizing these general-purpose FPSOs to commercializeour significant portfolio of offshore developments, we are able to deploy a safe and environmentally sound production system long before custom-design facilities can be ready, allowing the resource to come on-stream in a shorter time frame." North Sea rates pick up a little Offshore Shipbrokers Limited (OSL) in Aberdeen reports that here were a large number of fixtures over the weekend of 29/30 June, with rates rising to around GBP8,000-9,000 for cargo duties and GBP15,000 plus for rig moves.
|